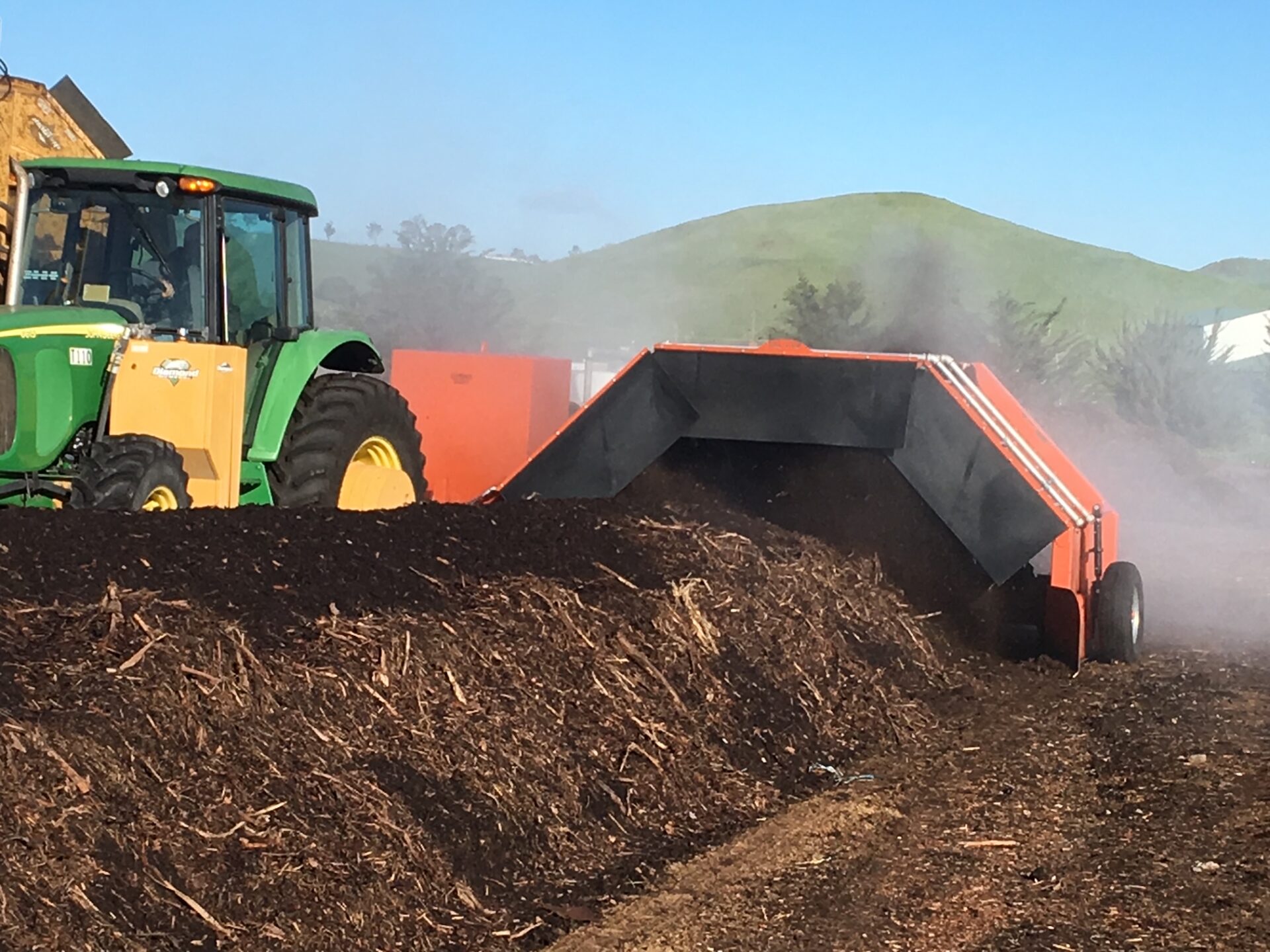
Compost offers a wide range of benefits to soils depending on the blend, providing soils with biomass, carbon and nitrogen sources.
In order for compost to work in a soil, it needs to have the proper blend of feedstocks and be tested/treated to ensure proper nutrient levels and microbial activity are present. This article provides insight into the large-scale compost operation at Cal Poly, San Luis Obispo, and how this compost provides benefits to a nearby vineyard.
Finding the Right Mix
Kevin Piper, Director of Agricultural Operations at Cal Poly, San Luis Obispo, said in recent video interview that the school’s own operation takes four key components into account when building the feedstocks that go into their compost: carbon to nitrogen (C:N) ratio, percent moisture, bulk density (measured in cubic yards) and texture.
“Good composting practices are important,” Piper said. “We want to know our feedstocks well, and that means knowing the specific components of each.
“Texture is a good thing to incorporate, and normally you’re going to get that with your carbon source,” he continued. “This could be anything from fine sawdust all the way up to rough woodchips. You want to find a happy medium; if you have too much fine texture, you’ll end up with a light mix that has a hard time holding temperatures, and if you have too much rough texture, you’ll end up with a density issue.”
The Organic Compost page on Cal Poly’s website (cafes.calpoly.edu/cal-poly-compost) says that the school’s operation removes solid manure from its dairy, beef, equine and poultry units and incorporates it with green waste from campus landscaping to create its unique blend. The specific feedstock breakdown for the operation, according to Piper, is green waste (55% moisture, 610 lbs/cu yd., C:N ratio of 150,) waste feed/silage (75% moisture, 1,300 lbs/cu yd., C:N ratio of 12,) horse manure (45% moisture, 450 lbs/cu yd., C:N ratio of 40) and separated solids from the on-campus dairy operation (85% moisture, 1,400 lbs/cu yd., C:N ratio of 18.)
“Once we’ve blended our recipe, we want our ideal component ranges to be a bulk density of 800 to 1,000 lbs/cu yd., 40 to 60% moisture and a C:N ratio of 30,” Piper said.
Best Practices for Compost
Creating a compost blend can be a complicated and drawn-out process and there are several safety/sanitation measures to keep in mind. If a compost producer’s operation is as large as Cal Poly’s, which Piper said produces 7 to 8 million pounds of manure annually that is then turned into about 3,000 to 3,500 cubic yards of finished compost, vigorous sanitation steps and testing are necessary to retain organic certification.
“Compost producers have to consider California’s regulatory environment,” Piper said. “In this state, we deal with CalRecycle and the Regional Water Quality Control Board, both of which have regulatory requirements for composting facilities. One of the main things to keep in mind when setting up an operation or composting in general is not to do it next to a wellhead or within a couple hundred feet of a live stream. This can pose issues of runoff.
“Another good [sanitation] practice is preventing cross-contamination by cleaning machinery between handling raw feedstock and ongoing/finished compost,” Piper continued.
Maintaining certain levels of microbial activity and nutrients within compost can also make or break an operation. Testing of temperatures and the product itself needs to be conducted before anything is sold. If a compost blend is not ready for use, according to Piper, it can be dangerous to incorporate into plants because of the potential for nutrient stealing.
“We have a pathogen reduction phase (PRP) in our windrow process,” Piper said. “We use short and long temperature gauges to get an idea of what is happening on the interior and exterior level of the compost pile. Once we’ve reached a temperature of 131 degrees F during the PRP, we have to maintain that temperature for 15 days and turn that windrow a minimum of five times. When there is a 20-degree differential between the interior and exterior gauges, we know it’s time to turn.”
Piper said that interior temperatures cannot exceed 150 to 160 degrees F in order for microbial activity to remain undisturbed. If they do, internal moisture conditions can become altered.
“When pulling back some of the compost after checking the gauges, we want to see a layer of white mycelium growing as it shows we have the right moisture conditions and a happy environment for beneficial organisms,” Piper said.
Before sending off finished compost samples to a certified laboratory, operators have the ability to conduct one last test to ensure for a stable product.
“We use a Solvita test,” Piper said. “It allows to test what we consider a finished product for ammonia and CO2 levels. If the test shows reassuring results, we can send it off to a certified lab that is tied with the U.S. Composting Council’s Seal of Testing Assurance (STA).”
According to the U.S. Composting Council’s website, the STA program is a “compost testing, labeling and information disclosure program designed to give you the information you need to get the maximum benefit from the use of compost.” Any grower looking to purchase compost for use in their own farming operation should look for the STA on a finished product.

Grower Usage
Jean-Pierre Wolff, principal owner of Wolff Vineyards in San Luis Obispo, Calif., explained in a phone interview his own usage of compost in his soils and the benefits it has provided him.
“I’ve been applying compost postharvest for 20 years and apply 1.5 tons per acre,” Wolff said. “It takes several years for compost effects to take place in terms of mineralization. In my case, in the first 10 years, I was mixing compost with gypsum. Now, I’ve switched to 100% compost to give priority to the carbon content. The benefit of the nitrogen content is a slow leaching, which has been a good approach for us in the vineyard to have a slow and steady feed of nutrients. It also increases microbial activity due to the higher quality of compost.”
Wolff switched to using Cal Poly’s compost mix in recent years for multiple reasons including its close proximity to his vineyard.
“Years ago, I used dairy farm compost from the Central Valley,” Wolff said. “Because of the transportation costs, I switched to green compost from Santa
Barbara county. Now, I use Cal Poly’s. I switched to them because they’ve gone through a lot of upgrades on their compost equipment and they also offered training classes. Close proximity was a big part of the decision.”
Even though the use of compost has been working out for Wolff’s vineyard over the years, he made it a point to note a couple of major tips when using and buying compost.
“One area which I think can be problematic because of climate change is that it [compost] only works well with areas of normal rainfall,” Wolff said. “I proved this during the latest drought. Utilizing drip irrigation just does not have the same flushing affect for nutrients into the soil as rain does. The microbe activity of freshly applied compost diminishes if this is the case.
“Not all composts are created equal,” he continued. “The whole business of it starts with the quality you get. It sounds fundamental, but it’s key. Always get compost from a reliable source.”
Producing and using compost is a complex process for both sides, and patience is required. Producers have to ensure that their final product is up to par (i.e. good feedstock sources, properly heat-treated, adequate nutrient levels and absence of any harmful compounds) and growers need to ensure that they are buying from the right source and utilizing good compost practices themselves.